Crown Equipment Corporation in Greencastle, Indiana needed an automated work cell capable of pressing and crimping bearings into an assembly to reduce the possibility of a workplace injury that the previous process presented. In the previous assembly process the operator pressed bearings into the upper tube of the steering column. However, the press that was being used for this operation was ineffective at pressing together the parts and was only used for the final crimping. As a result, the operation posed ergonomic and safety risks as it required the operator to line up and hammer in the bearings before the pressing operation occurred. This project eliminated the safety and ergonomic issues associated with the previous process by automating the process and introducing a new press. As a result, an operator only has to load and unload parts in a designated safe area. This project vastly improves safety and ergonomics as well as reduces cycle time, resulting in cost savings.
Semester of Project:
Team Photo:
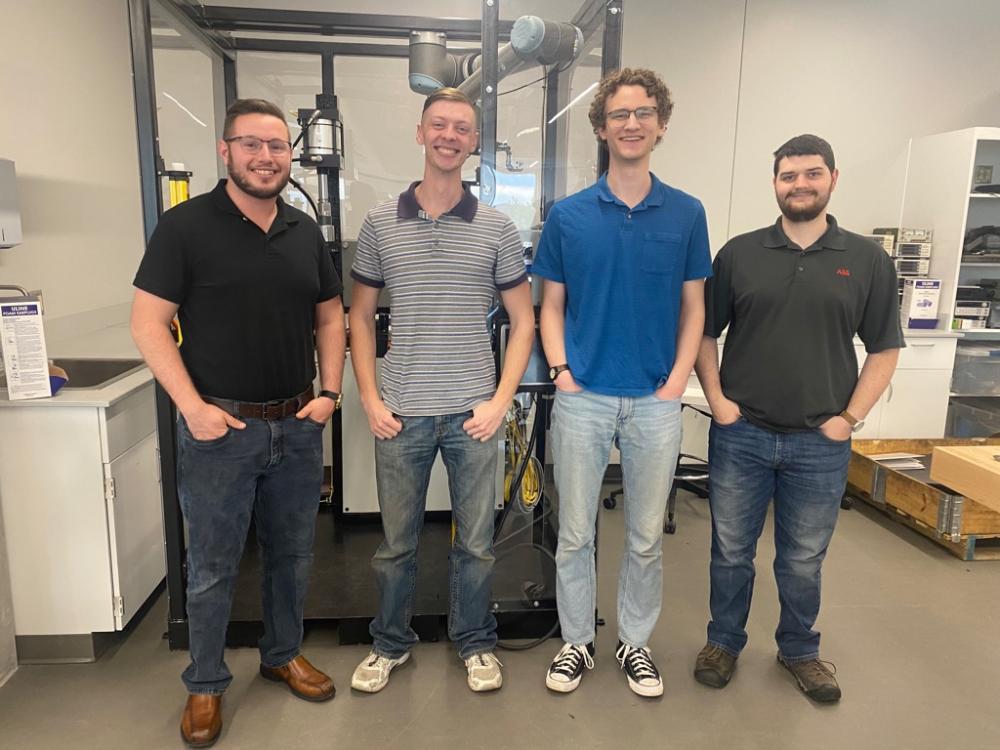