BorgWarner must routinely perform a type of test known as Salt Spray. The test involves strapping the device under test, henceforth referred to as the DUT, into a test fixture to secure the DUT in place. The DUT and fixture are then placed in a sealed test chamber and sprayed with salt water to simulate conditions a vehicle may experience near large bodies of salt water. While the DUT is expected to survive the test undamaged, the problem involves the amount of both physical and monetary waste generated from performing salt corrosion tests on 6061 billet Aluminum at BorgWarner. During these tests, the fixture will become covered with salt and degrade it until it is in an unusable state, thus making scrap. Because these fixtures can cost upwards of $9500, being able to reuse them even once would lead to significant cost savings for the company.
As the fixtures come in many different shapes and sizes, the cleaner will need to be able to support these diverse sizes and weights while effectively removing the salt on them. Products like this exist, however, for the company’s purpose, a more specific and cost-effective solution is desired as these machines are expensive to purchase and maintain. Additionally, the device needs to be an all-in-one system to allow it to be easily moved.
If the ability to reuse these fixtures were to be achieved, the issue of having to wait for additional fixtures to arrive could be circumvented for a time. This would in turn allow the technicians to perform their tasks faster as the supply of fixtures would not decrease as rapidly as they do currently.
Semester of Project:
Team Photo:
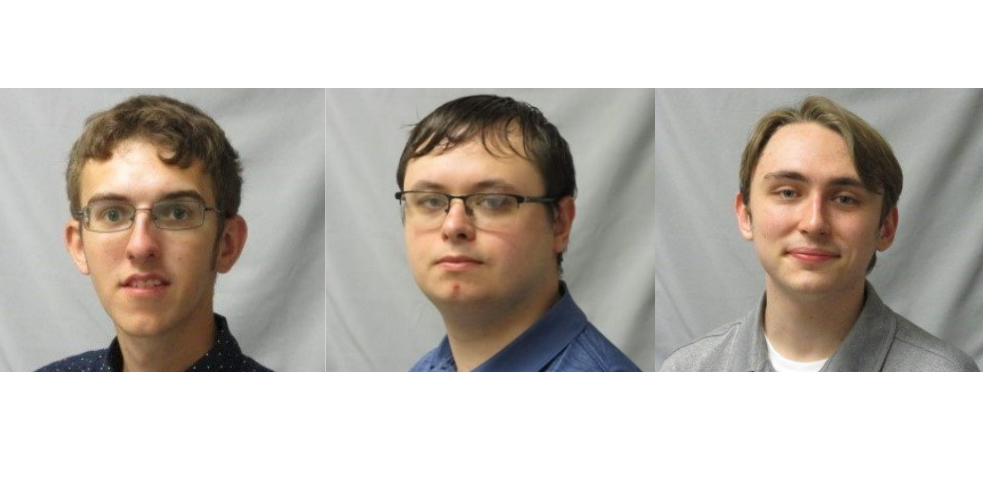