As it stands in the metal casting field, humans are still used to manually spotting defects in parts on a line in order to tell when the dies for said parts are failing or starting to fail in some regard. This consumes lots of time and money as there are more employees that must be staffed and paid, along with the limitations of humans that can both miss defective parts and be slow in the analysis of them. Due to this, companies are paying more than they would need to be to watch for failing dies. Our project aims to save companies money by eliminating this need and automating the process. Our automated system aims to replace or limit the human inspectors with a 2D camera system that will photograph cast parts and be able to spot when parts are starting to show defects. This would then be a sign for the human operators to address the d and see if they need replacing. This would save the company money as they would no longer need as many employees, while also making the system both more accurate and efficient with our new automated system. Having this faster system will bring benefits to all as a faster and more accurate line increases the production of parts in tolerance for the end user to purchase. While increasing company profits, they will have fewer defective parts produced as they will be identified quicker to advise a change of die.
Semester of Project:
Team Photo:
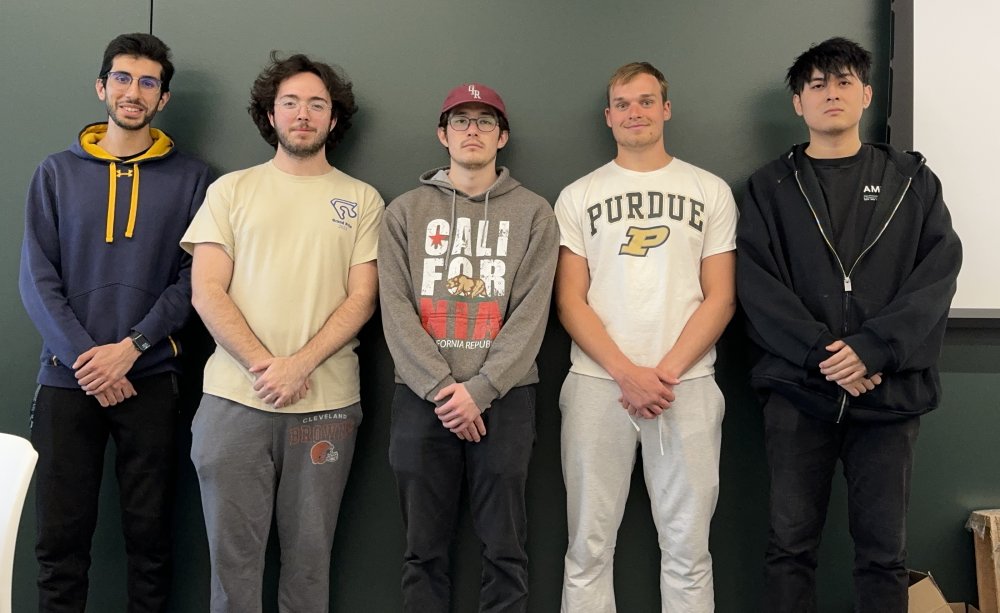