Last month, Purdue Polytechnic faculty and executives gathered with representatives from Capture 3D/Zeiss, Howmet Aerospace and with peers in the industrial engineering program at Purdue to celebrate the recent installation of a Zeiss ScanBox 5120, that was made possible through Howmet Aerospace Foundation.
What the ScanBox does
With its ScanBox products, Zeiss has become an important player in the applied and industrial applications of metrology, the science of measurements. Purdue Polytechnic’s leading faculty member in this field is Paul McPherson, a professor of practice in engineering technology who facilitated many relationships in order to acquire and house the ScanBox for use in multiple courses, including one where students will receive certification on the machine.
“This machine allows manufacturing facilities to scan manufactured parts and then overlay the scan to the ‘perfect’ digital version of the model to determine how in or out of specification the part is,” McPherson explained. The ScanBox’s camera is capable of capturing 12 million individual points per scan, and since it is attached to a programmable, moving arm, it takes multiple scans from many angles and turns it into a digital “mesh.” This mesh can then be used to reverse engineer a component or compare it to the computer-aided design (CAD) model.
Scanning technology of this kind has wide industrial applications, from creating accurate parts for automobiles and planes, to crafting near-flawless molds in the metal casting and manufacturing process and beyond. The ScanBox supplies a learning opportunity for faculty as well as students, as this particular method of metrology is more heavily automated than many of the alternatives that have been available on campus.
Increasing collaboration across colleges
“From my industry career, I’m a construction management person. And I can tell you—I love 3D scan technology like this,” Daniel Castro, Purdue Polytechnic’s dean, said. “It’s totally revolutionized construction. And if this gift is any indication, it’s doing it all over again in manufacturing.”
At present the ScanBox is meant to serve as a foundational training device in multiple metrology courses and will provide the opportunity for a certificate program. This program is most useful for students in Purdue Polytechnic’s mechanical engineering technology (MET) and manufacturing engineering technology (MFET) majors. However, since advanced metrology is equally useful for students in Purdue’s College of Engineering—particularly in their School of Industrial Engineering (IE)—IE students have the opportunity to take the same course alongside their peers in MET and MFET. This will count toward IE’s minor in manufacturing.
“In STEM, technology is really the practical application of science, math and engineering,” said, Ken Burbank, head of Purdue Polytechnic’s School of Engineering Technology. “And an investment like this from Howmet, who Paul has introduced us to, really shows the depth of Purdue’s commitment to technology. This piece is going into the single largest teaching space on campus.”
The ScanBox resides within industrial engineering’s “Build @ Scale” lab, housed within Lambertus Hall. This marks the first instance of cross-pollination in a physical teaching space between Purdue Polytechnic and the College of Engineering since the building’s dedication, where deans of both colleges remarked that Dudley and Lambertus Halls should be a place of collaboration among students and faculty.
Preparing students for the future of work
Josh Smith, the engineering manager at Howmet’s La Porte, Indiana location, said that having a pool of recent graduates with some preexisting training in advanced metrology would be “absolutely massive” for the company. “We are going further and further into the 3D modeling, CAD space,” Smith stated. “But frankly, we have this noticeable gap in education. A lot of universities have people with experience, but they don’t actually use it. Or they’re not willing to invest in the technology itself.”
“It’s a big deal that Howmet invested in us, because you’re talking about a single piece of equipment that would be half-a-million dollars at full retail value,” McPherson added. “And it’s the cost of entry with this technology, as well as the small pool of people who are willing to adapt to it which have made this so rare in education. As far as I know, we’re one of the first colleges to have this particular piece in an undergraduate teaching lab—maybe even around the world, that’s how rare this is.”
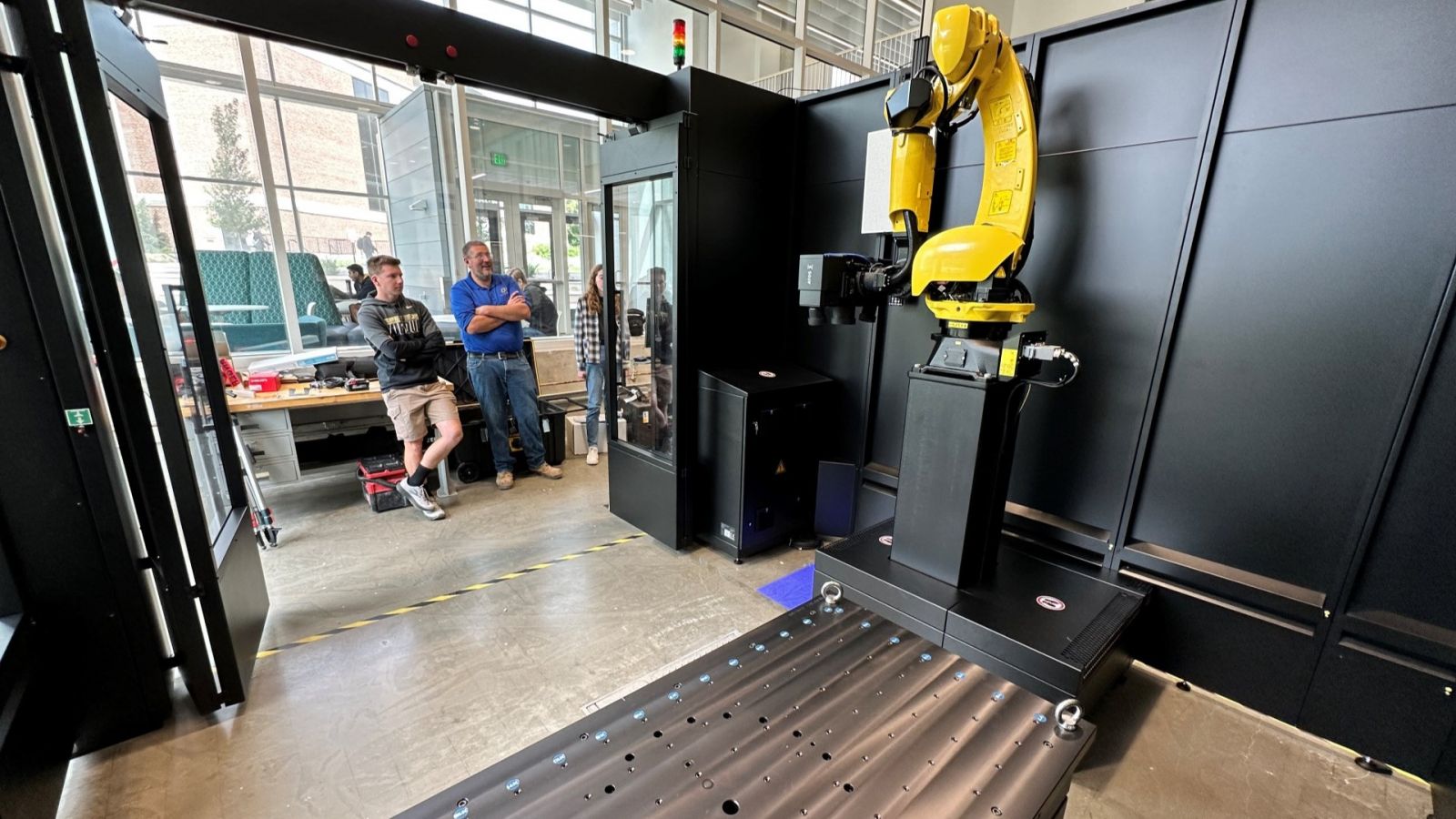
Smith also emphasized that Howmet is looking to do more than just fast-track new employees by giving them a head start on certification and training. He hopes this will also provide “longevity and long-term success” as employees get into their roles. “I think for us, we’re just going to see a higher success rate, where we’re putting the right person in the best position for them. They can enter a role with some expectation of what they’re getting into. At present, it’s kind of a black box because students aren’t exposed to 3D capture technology to this level.”
Regarding future collaboration with industrial engineering (including students, faculty and School Head Young-Jun Son, who was also present), McPherson looks forward to “continuing onward, I hope for years to come.”
“For both of us, it’s all about updating the equipment we all teach on to the latest and greatest, right? So it was very positive, and really a no-brainer, to get both colleges involved and to work out teaching opportunities that both parties wanted to say ‘yes’ to.”
Additional information