Smart Manufacturing Industrial Informatics
Smart Manufacturing Industrial Informatics
Transform the Future of Manufacturing with Smart Manufacturing Industrial Informatics!
Are you passionate about the convergence of digital and physical worlds in manufacturing? Do you aspire to lead the next wave of industrial innovation with smart technologies? Purdue University's Smart Manufacturing Industrial Informatics major is your gateway to a dynamic and impactful career in the world of smart manufacturing.
In this major, students gain hands-on experience with advanced manufacturing technologies, IIoT, cloud computing, and machine learning. They develop skills in industrial networking, process control, CAD/CAM programming, modeling and simulation, mixed reality applications, and additive manufacturing. The program also emphasizes automation, human-robot systems, data analytics, and real-world problem-solving through team projects and capstone experiences.
Why Choose Purdue's Smart Manufacturing Industrial Informatics Major?
- Innovative Curriculum: Our courses cover a wide range of topics, including smart manufacturing, IIoT, cloud computing, machine learning, automation, and robotics.
- Hands-On Learning: Our program emphasizes practical experience through real-world applications and problem-solving. You'll gain proficiency in using advanced manufacturing technologies, cloud computing, and machine learning to optimize manufacturing processes.
- Industry Connections: Benefit from Purdue's strong ties with leading manufacturing companies.
- Career Opportunities: Graduates are well-prepared for careers in industries such as manufacturing, automation, data analytics, and industrial informatics. You'll have the skills to design, develop, and optimize smart manufacturing systems, making you a valuable asset in the workforce.
Embark on a journey of innovation and excellence with Purdue University's Smart Manufacturing Industrial Informatics major. Our program is designed to provide you with the knowledge, skills, and experience needed to thrive in the ever-evolving field of smart manufacturing and industrial informatics.
Program Details
Potential Employers
Microsoft
PTC
Rockwell Automation
General Mills
Potential Job Titles
Manufacturing engineer
Manufacturing data analyst
Process engineer
Smart factory manager
Where You'll Learn
The manufacturing engineering technology program is accredited by the Engineering Technology Accreditation Commission of ABET, https://www.abet.org, under the commission’s general criteria and program criteria for Manufacturing Engineering Technology and similarly named programs.
EVERY GIANT LEAP STARTS WITH ONE SMALL STEP
Course Highlights
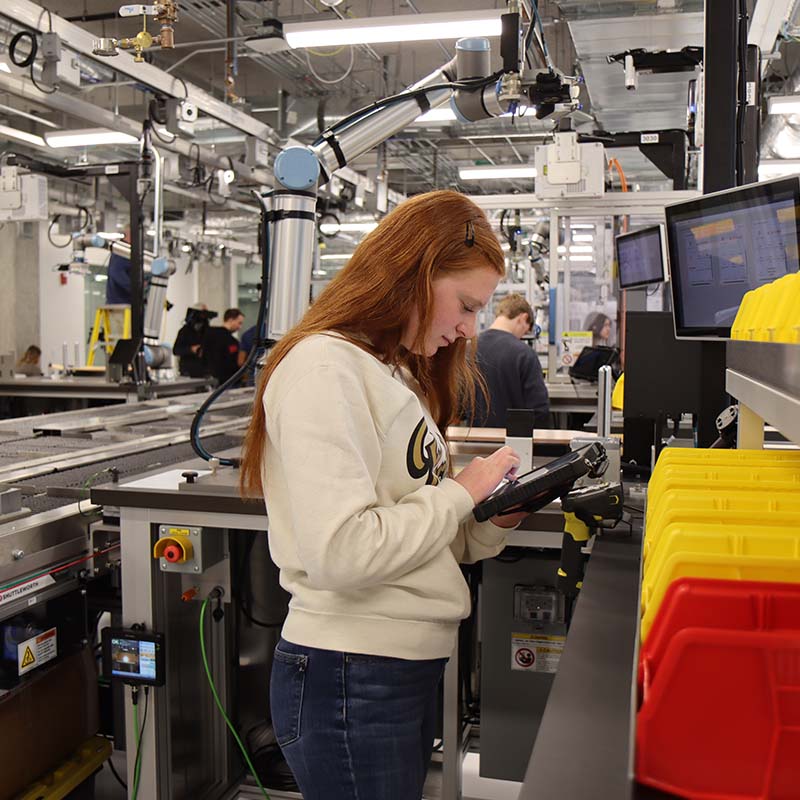
Academic Opportunities
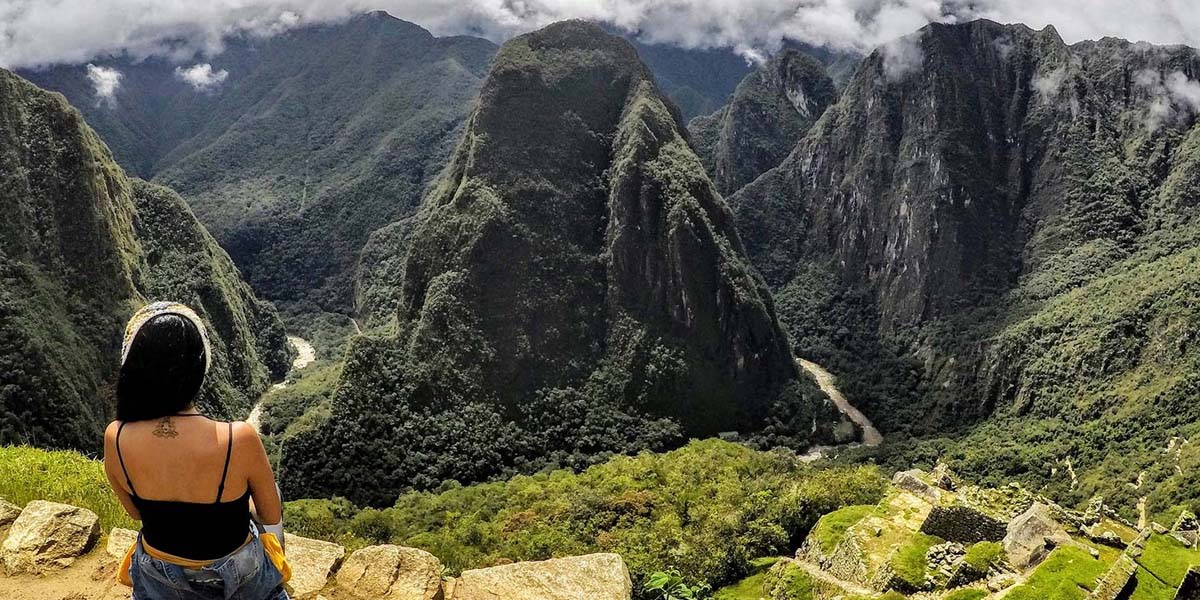
Study Abroad
All students in the Purdue Polytechnic can choose to gain an enriched perspective of the global marketplace through a multitude of global experiences that both interest and benefit the student.
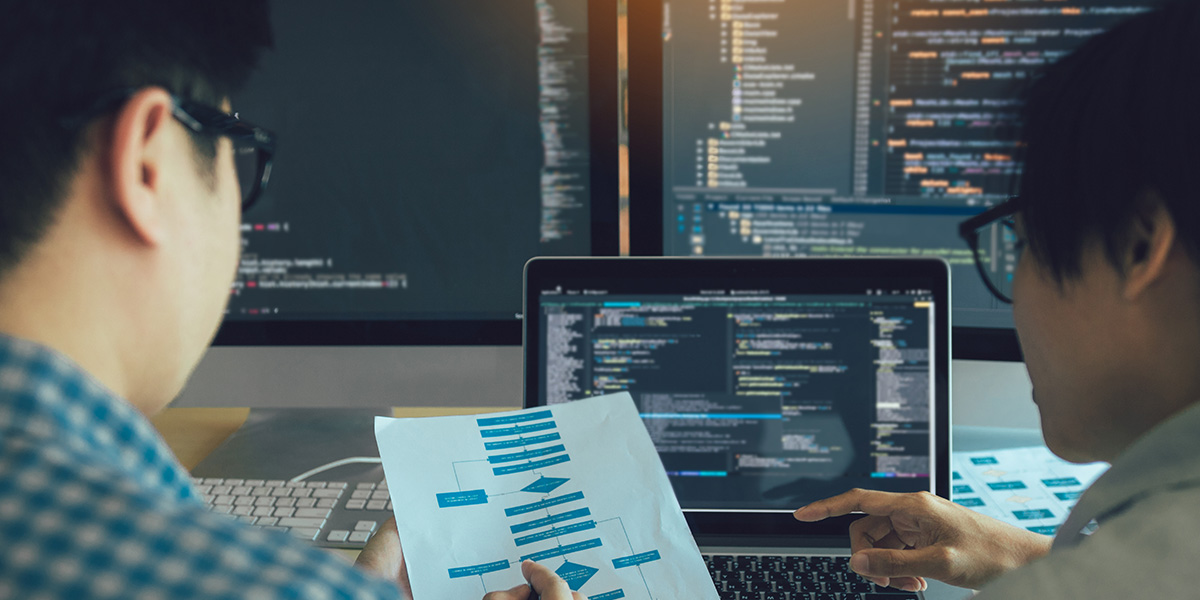
Minors
Purdue Polytechnic offers minors that provide unique opportunities to expand your knowledge, broaden your experience and prepare you for success after your time at Purdue.

Student Organizations
Student activities and organizations are a great way to immerse yourself in your chosen path of study. Choose from a variety of interests within the college organizations or university-level programs.
